Printed circuit boards, or PCBs, are used to mechanically support and electrically connect electronic components using conductive pathways, tracks or signal traces etched from copper sheets laminated onto a non-conductive substrate.
Used in quantities of millions, in 2018 the Global Single Sided Printed Circuit Board Market Analysis Report estimated that the PCB market would reach USD 79 billion by 2024.
PCBs are generally made of various layers of materials, which are bonded together by heat, pressure and other methods. Its basis, the so-called substrate, is commonly made of glass epoxy, also known as fibre-reinforced plastic.
In order to ensure and achieve an efficient and smooth PCB manufacturing process, a top-quality and flawlessly woven glass fabric is the key to minimized rejection costs and ultimate quality assurance.
A fully integrated PCB manufacturer can control the entire manufacturing process. One of the world’s largest manufacturer of such boards and other technical glass fabrics, operating several plants in China and Taiwan, occasionally experienced the tiniest unevenness on the surface of its PCB boards.
Particular defects originated from exactly that woven glass fabric, eventually caused by minute filamentation of the yarn and slightest fluff accumulation during the weaving process. By using FALCON-i optical sensors to monitor the weft insertion during the weaving process, such tiny yet costly defects could easily and reliably be eliminated.
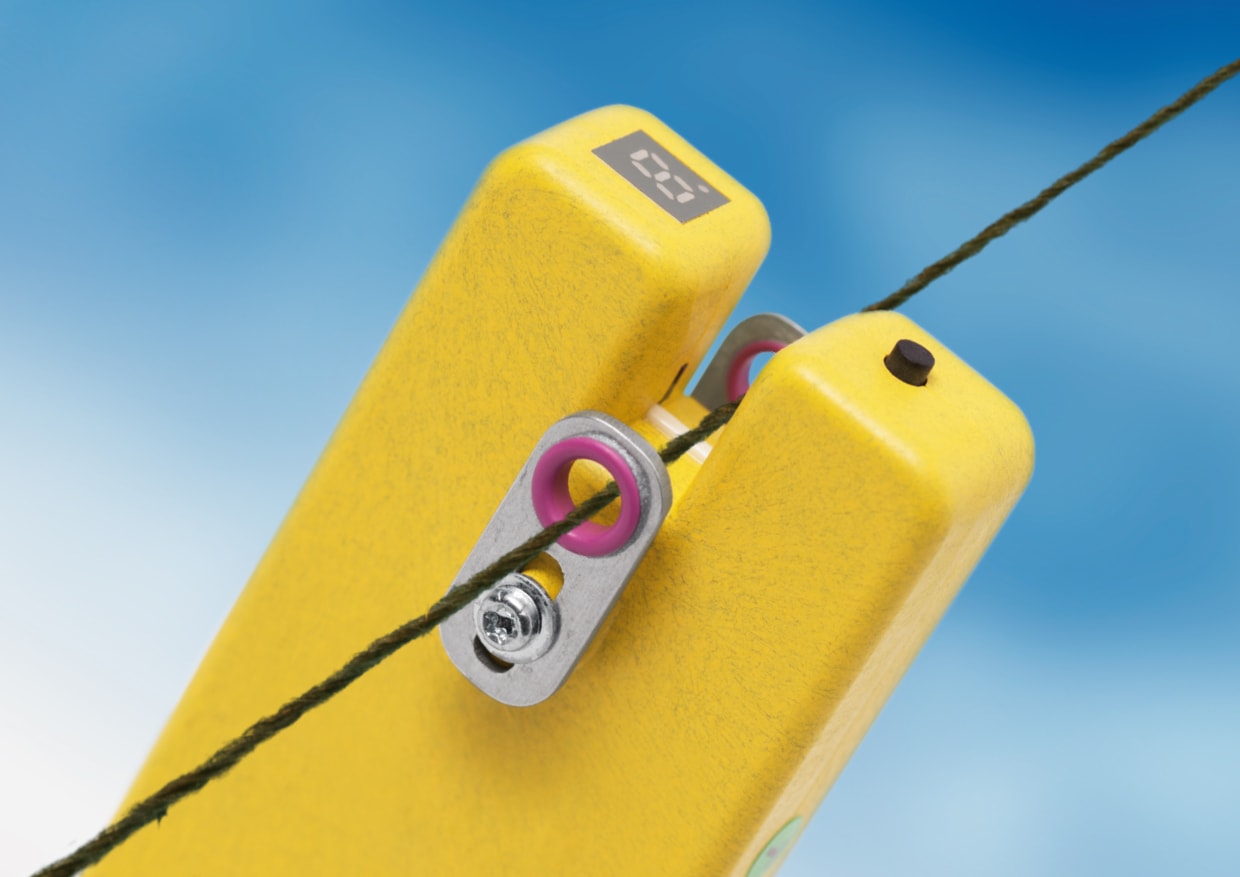
In order to detect even the tiniest yarn irregularities, FALCON-i offers extensive sensitivity levels, allowing customers to fine-tune the ratio of machine stoppages caused by necessary quality control stops.
Any manufacturer of demanding technical fabrics and composite textiles used in applications such as PCB manufacturing, automotive, architecture, filtration, aeronautics, medical and carbon industry can highly benefit from this type of versatile quality monitoring sensor.
The implementation of FALCON-i optical yarn defect sensors in the quality control of any running yarn throughout the manufacturing process of fabrics is simple and easy.
FALCON-i’s unique flexibility to select the level of quality control enables technical fabrics manufacturers to respond quickly and flexibly to market trends, demand and developments.