All seven days from June 8th to 14th were highlighted by a stream of visitors to the Dilo stand which gave prominent attention to a complete production and demonstration line of MicroPunch technology.
On this stand of 750 sqm, with 36 associates of DiloGroupin in attendance plus external services, the complete line demonstrated the brand new “MicroPunch” technology from bale opening to end-of-line winding.
The MicroPunch features had been promoted in advance at INDEX to make interested parties acquainted with the features of high-speed lightweight needling. Several press releases and official presentations including one at ITMA announced this breakthrough for significant energy savings.
All visitors have confirmed that the current commercial and environmental issues concerning sustainability, critical energy supplies at increasing prices, shrinking of water reserves as well as the outlook for fibre material savings should attract our utmost attention.
These concerns find an answer in the field of lightweight nonwoven production through Dilo’s brand-new MicroPunch production technology which will become relevant when investments take place for nonwoven production in a weight range between 30 up to more than 100 g/sqm.
MicroPunch offers a tremendous savings potential for electrical energy and energy from gas heating as no water is consumed. Furthermore, there is no fibre loss associated with this production technology since trimmed material can easily be recycled within the process.
It has been illustrated that depending on the individual costs for electric power, gas and water, production cost savings may be as high as 25 % associated with around 40 g/sqm and even up to 50 % for products around 100 g/sqm.
The MicroPunch line consisted of DiloTemafa fibre preparation, opening by a BALTROMIX bale opener, carding willow and dosing opener of the latest design followed by the successful DiloSpinnbau MultiCard fed by a universal card feeder including the new IsoFeed system for reduced weight variation.
IsoFeed can add the correct amount of staple fibre volume in areas of lower mass in the flock mat plane, thus correcting weight deviations and improving the overall CV value by ca. 4 %. The very regular web mass at the end of the card allows a reduction of the average weight by approximately 10 % resulting in considerable fibre savings when a minimum weight associated with a high regularity must not be exceeded.
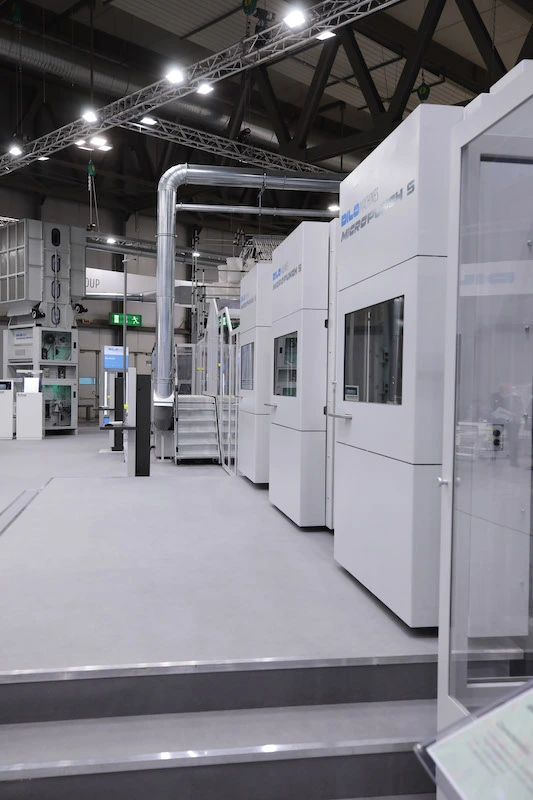
The MultiCard was additionally equipped with the new “variogram and speed controller” which allows an optimum of gap and speed adjustments at the fifth worker and at the doffers. The web quality during the show impressed by superior regularity. This is particularly important when no crosslapper is used as was the case at ITMA where the card fed the following needle-punching equipment directly.
The Dilo team installing this complex line within 10 to 12 days including commissioning demonstrated its capabilities under high time pressure. It gave an example to all involved with their efficiency, coordination and professional attitude.
This resulted in a great performance and added to an excellent atmosphere during these days together with our range of customers and interested parties. This line will be shipped back to our research and demonstration centre were DiloGroup will use it for product development and also in cooperation with our customers and their specific fibre and requirements.
The second highlight of DiloGroup’s ITMA demonstration was the introduction to our cooperation with Messrs. Dell’Orco & Villani and Technoplants for “RecycloLine”. “RecycloLine” is the platform for the three companies involved to engineer and supply complete lines for mechanical recycling of garment waste in order to fulfil current and future requirements to save valuable fibre material instead of wasting, burning and dumping it.
DiloSystems as a general contractor will coordinate the engineering of individual projects for our customers worldwide and will be offering demonstrations of tearing, and aerodynamic web forming, through air bonding, carding, cross lapping, needling as well as air systems engineering which is to control excessive amounts of dust in such production lines.
Our engineering will also comprise end-of-line cutting, winding, palletizing and packaging. Our customers will be informed and included in the engineering process in order to decide which method of web forming and consolidation works best for their particular purpose, its quality and economics.
Four demonstration locations in Florence, Ancona, Pistoia (all Italy) and Eberbach (Germany) are available to offer a deep insight into this particular technology including sampling of material from recycled fibre.
ITMA attracted also for this field a lot of visitors who have discussed the features of recycling lines in detail with our experts.